Supplier of steel slag processing equipment
Slag is suit for high-performance cement and concrete admixtures to improve the performance of concrete. Concrete mixed with steel slag powder having a low heat of hydration, corrosion resistance, and reinforced strong bond, post-high strength, anti-miniature and other characteristics, can be widely used in dam engineering, underwater engineering, road works, anticorrosion, large-scale construction projects, more and more by the construction industry, the transportation industry's favor. Therefore, there is market demand for domestic products of the project a lot of room, great market potential, feasibility strong, broad development prospects.
steel slag powder is used in cement production, can play a superior performance in many aspects:
1, steel slag powder is a superior performance of concrete admixtures, adding 10 to 35 percent of the powdered slag in the concrete, while the incorporation of 0-20% finely ground steel slag and from 0 to 9% silica fume, substituted 10 to 50% of cement and cementitious materials in a total amount of 380 ~ 550 kg / m3, you can configure the C20 ~ C60 concrete.
2, steel slag can be incorporated into a single concrete, but also with slag powder, fly ash, silica fume concrete composite incorporated. When incorporated into the slag alone to about 25% of steel slag powder instead of highest intensity when the cement concrete. For late strength of concrete steel slag growth more favorable.
3, Shougang mixed finely ground steel slag concrete mixed with a higher strength than the fly ash concrete; with the powder slag concrete considerably.
4, adding Shougang powdered slag concrete strength concrete strength in line with the general rule, therefore, mixed with finely ground steel slag concrete mix design fully in accordance with usual methods and specifications to carry out.
5, mixed steel slag concrete slump minor damage, but also with admixtures related.
6, Shougang incorporated finely ground steel slag can greatly reduce the heat of hydration of cementitious materials, which reduces the heat of hydration and effect quite alone with fly ash, slag powder is superior.
which Slag processing equipments is best? What about the production process?
It is understood that, due to the high energy consumption of traditional slag ball mill , do not meet environmental protection requirements of today's social development and will be phased out, the new environmentally friendly slag vertical mill has become widely accepted slag processing equipment, which is provided by hot air drying stove. Its production process is:
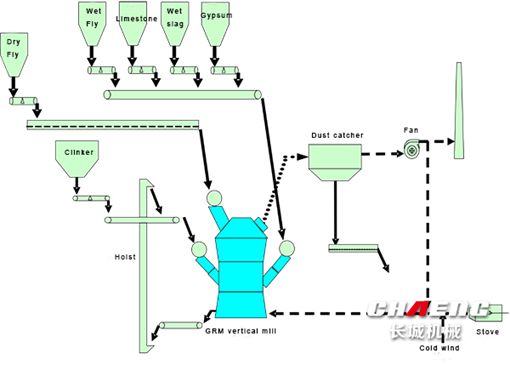
First, impurities, chunks separated, and in addition to iron, by the vertical roller mill grinding using vertical mill hot stove provided, drying and grinding process to achieve, qualified powder into the flour library is finished.
Secondly, the space under the belt material to climb transit hug, hug with a shaker transit impurities and mass separation. After preliminary intermediate magnetic separator iron. In transit hug belt conveyor disposed under the screen in addition to the ingredients delivered to the warehouse after impurities and chunks. To prevent non-magnetic metal block into the mill, belt conveyor provided with metal detectors. Ingredients warehouse at the end with a flat belt scale. To prevent the blocking positions, set two vibrator warehouse wall to prevent clogging.
Again, after dosing scales, by the belt conveyor (electromagnetic separator is provided on the belt conveyor) into the grinding plant. Material from the warehouse to the gate via the hydraulic lock three vertical wind mill feed drying, grinding and separator, hot air drying is supplied by the stove. Workshop for the vertical mill grinding system of roller mill, feed mill is grinding rolls stand on a rotating disc to be crushed, be crushed under a certain load, the hot air after grinding, that rise into the air carrier efficient vertical mill is located on the top of the separator, sorted coarse and fine. Fines (ie refined) from the air into the bag filter to collect, transport equipment to a flour store via chutes, hoists and the like. On the mill separator disc falls again elected meal grinding in order to save energy and iron, part of the meal is discharged from the disc perimeter overflow device via recycled materials vertical mill bucket elevator, pneumatic two-way valve, dry powder Permanent magnetic drum separator, etc. In addition to iron again returned to the mill grinding cycle stand. After collecting the exhaust gas after the exhaust fan into the chimney, as part of the larger hot air and circulating air stove produced mixed into the vertical mill drying, and the rest into the atmosphere.
Finally, the powder from the grinding plant by bucket elevator, library top chute into the powder stored in the library. Library with pink inflatable cone decompression library, will ensure smooth cutting and a certain homogenizing effect. Powder storage using 4-Φ15 × 35m of reinforced concrete silos, reserves of about 4250 tons / month. Bulk powder reservoir bottom fitted with equipment for cars exported in bulk powder.
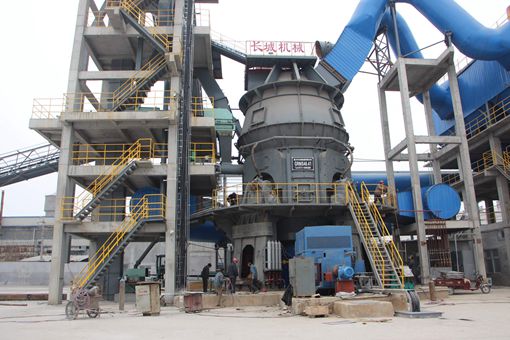